Stage 1: Clay Sculpture
The creation of this striking bronze began just like many other Tim Huhn’s, with an established and meticulous workflow. While the original Unknown Worker went through many study phases until it was refined into the emblematic piece it is today, the bronze started out as a grayscale version of the painting, which was scaled and subsequently printed as a reference for the final sculpture. The next step was to form the internal aluminum armature in order to support the clay-work. As expected, this structure closely resembles the concept of a human skeleton, giving the sculptor a general idea for the pose and volume of the piece. Once these aspects have been determined, a layer of thinner wire is wrapped around the skeletal shape in order to provide a stable surface area for the clay to be worked on.
Unlike water based clays, the plasticine oil clay used for this step does not fully dry, allowing for the artist to make modifications throughout the whole piece as it develops. Once the correct clay volume has been reached for the piece, the detailing phase begins. This stage goes through both, additive and subtractive processes. In other words, extra clay is added, as well as removed from certain parts in order to create the extraordinary depth and textures all around the piece. Once every detail is just right, the clay sculpture is ready to start the molding phase.
Stage 2: Rubber Mold
At this stage, the clay sculpture goes to the bronze foundry where the rubber molds will be made. Because of the complexity of this sculpture, Tim Huhn worked with Genesis Bronze located in Paso Robles, California; their reputation for artistry and attention to detail is unparalleled, and Tim knew that they would be able to cast the strength and integrity of “The Unknown Worker” with the right patina finish. Depending on the complexity and anatomy of the sculpture, separate molds will be created for different parts of the sculpture. In the case of Tim Huhn’s Unknown Worker, the arms, rod, gears and other small details such as the rag in the back pocket were all casted separately in order to ensure a perfect mold impression. This first mold is created out of rubber. During this process, a system of keys is placed in order to keep every layer consistent. Once this stage is done, a fiberglass mother mold is created around the rubber in order to increase its structural stability and prevent the rubber from shifting or deforming. This shell resembles a clam like structure with a parting line in the middle which is later separated in order to reveal both halves of the rubber layer. This is done separately for all the limbs and accessories which were casted separately as well.
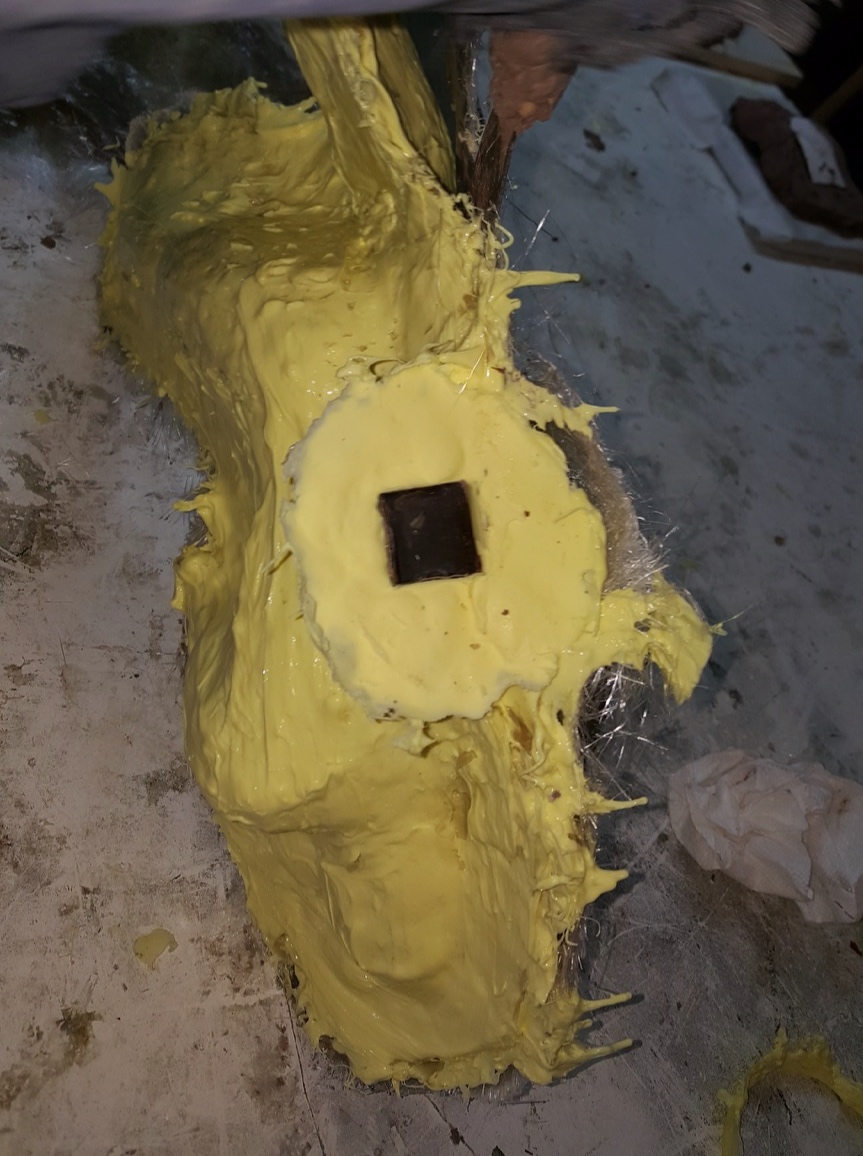

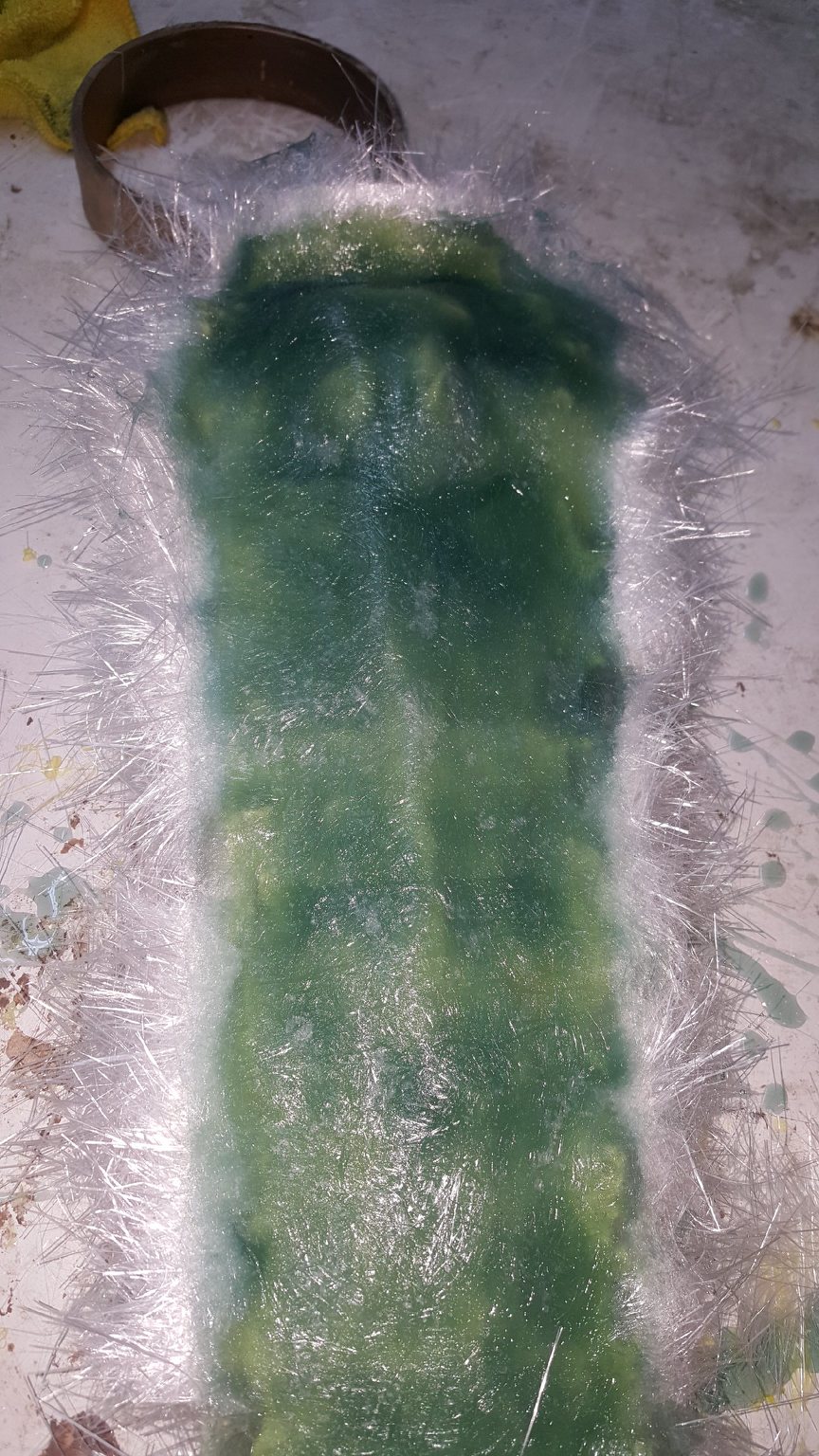
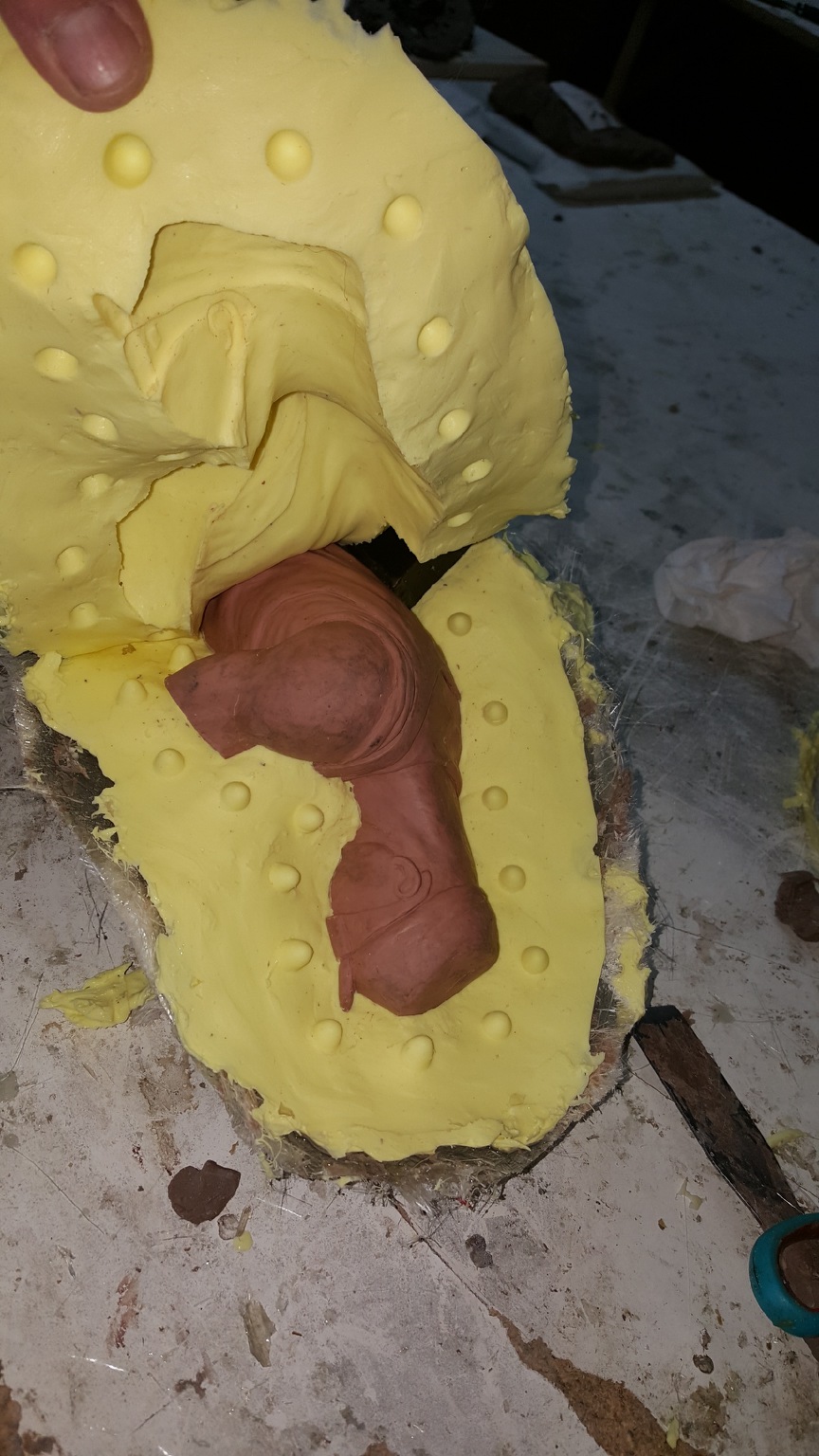

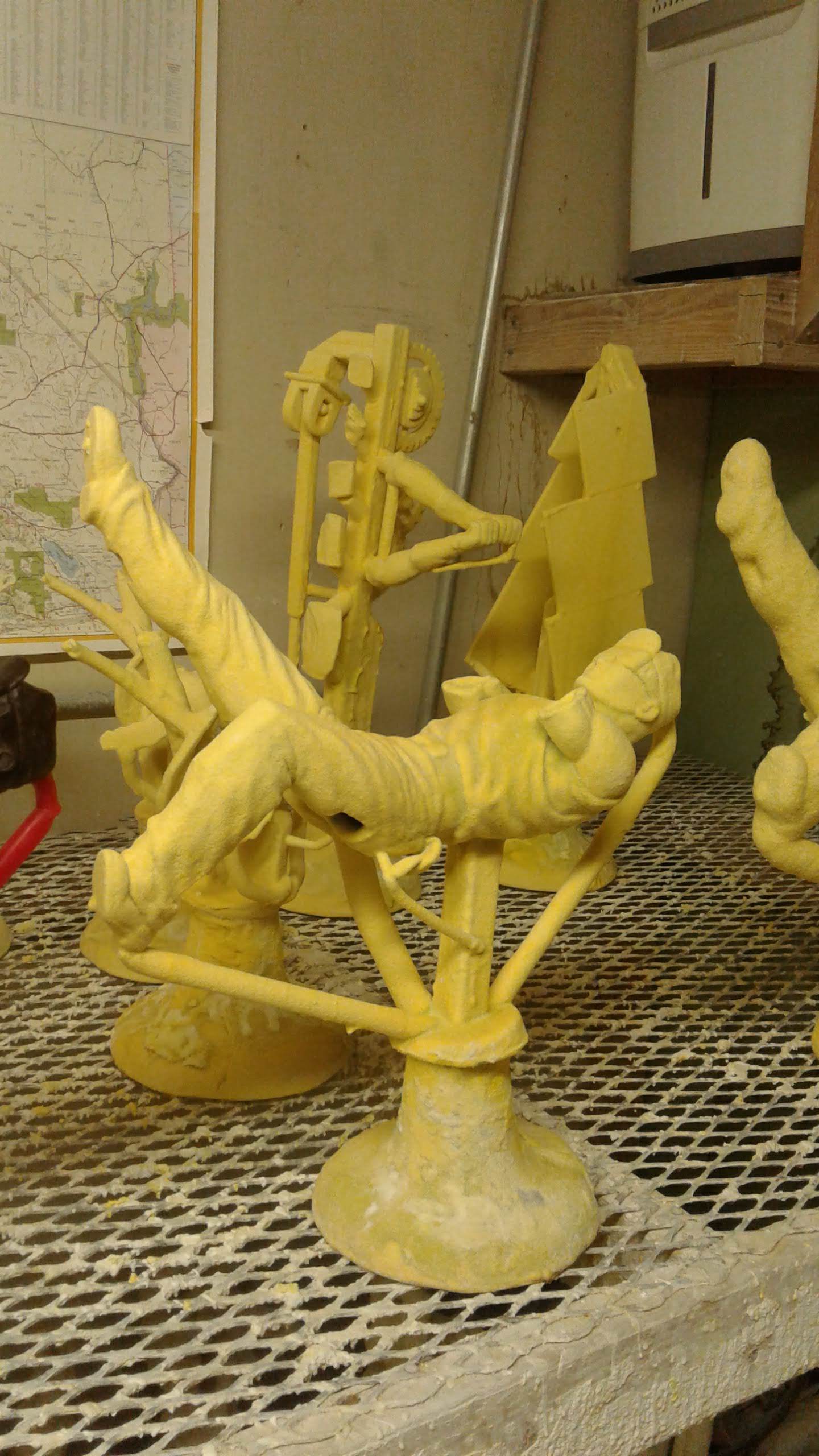
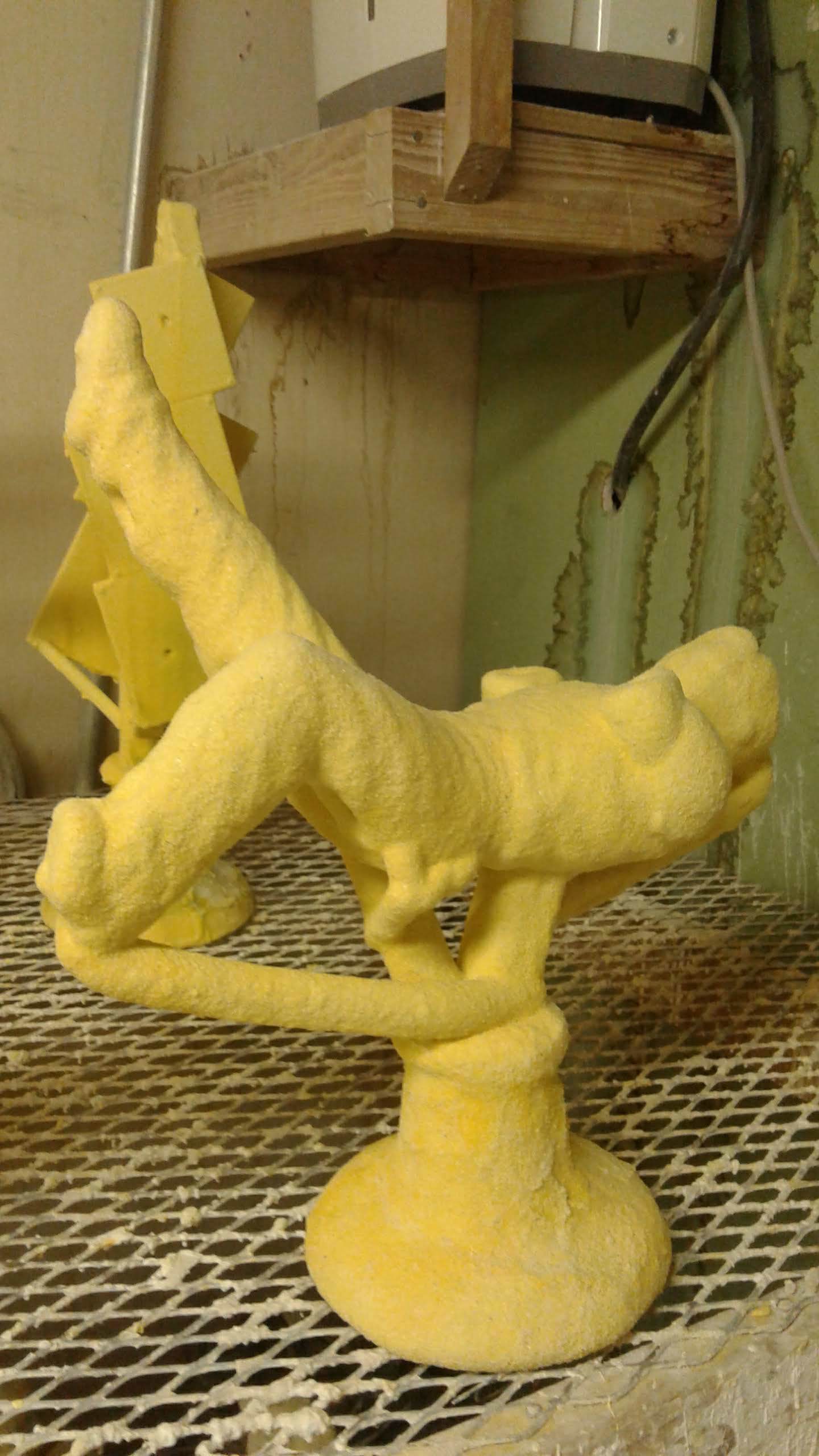
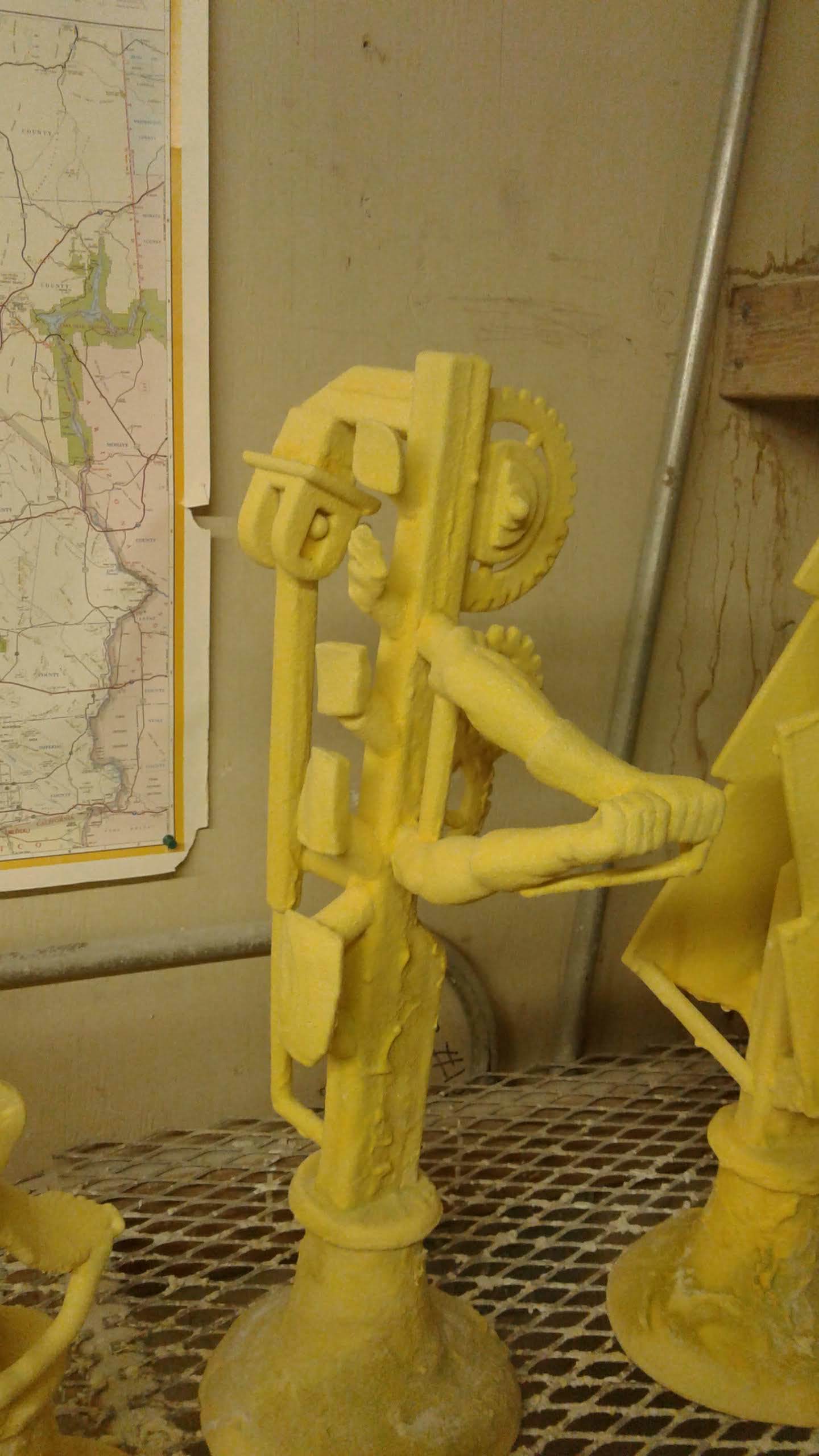
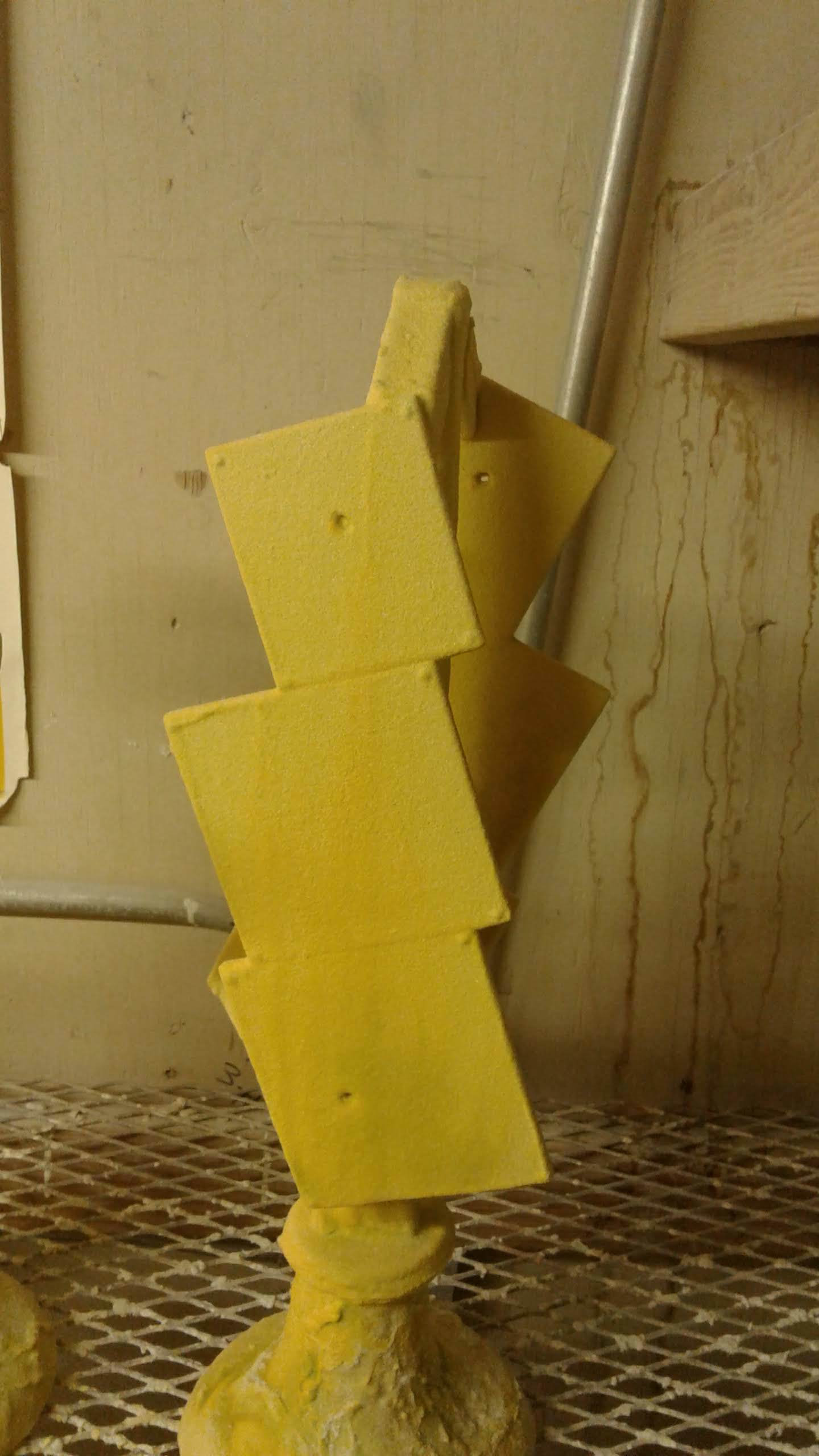
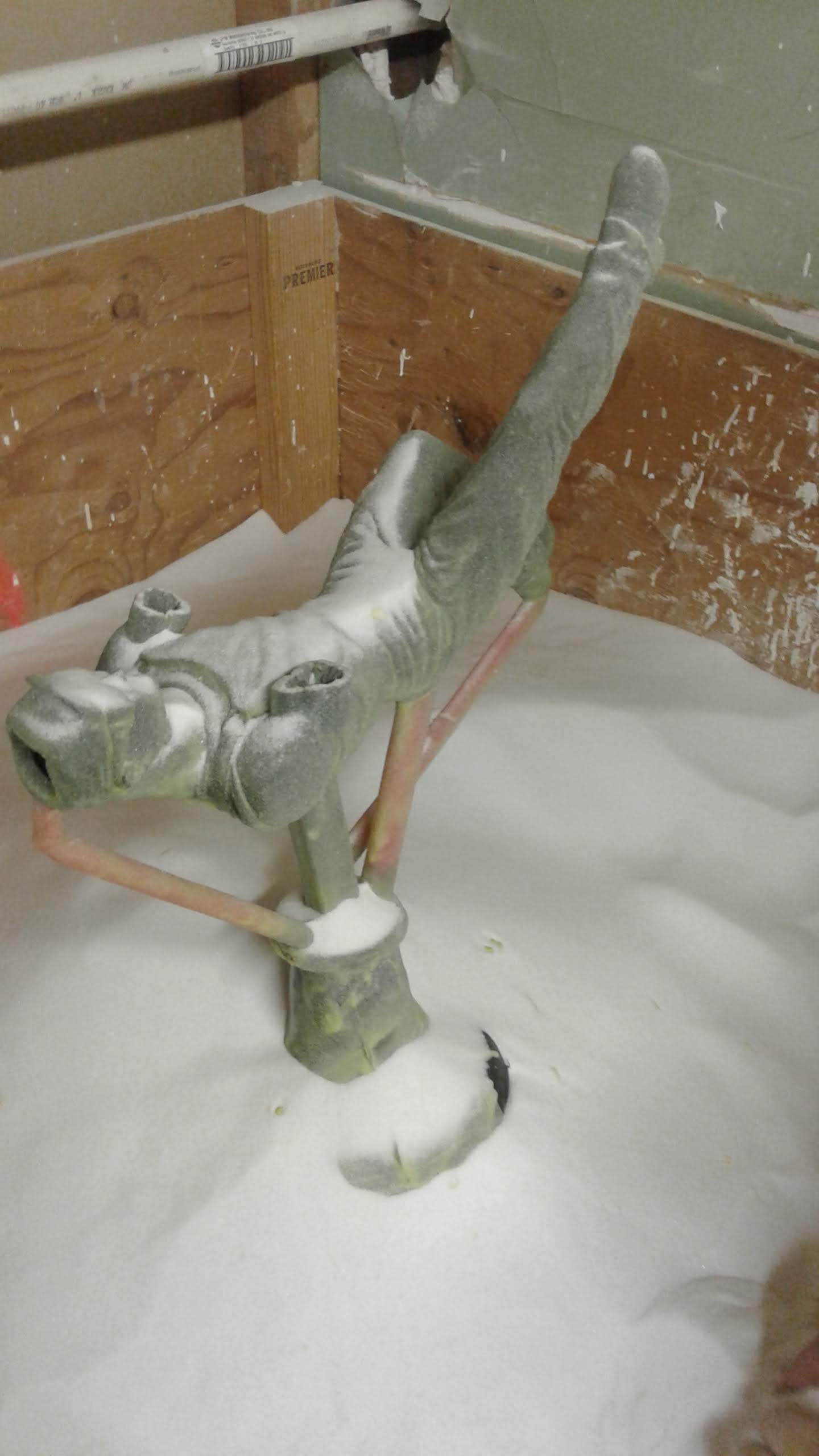
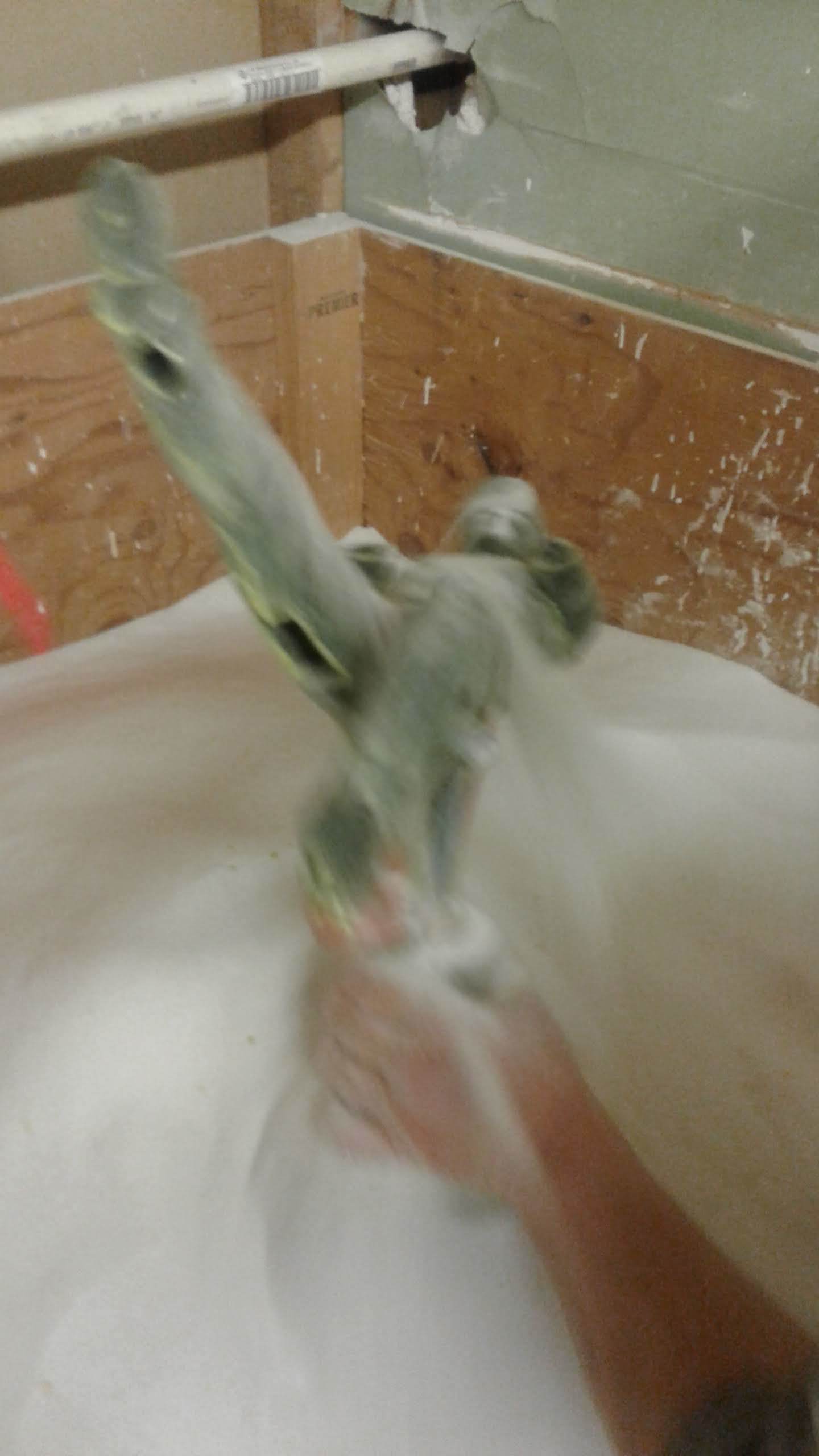
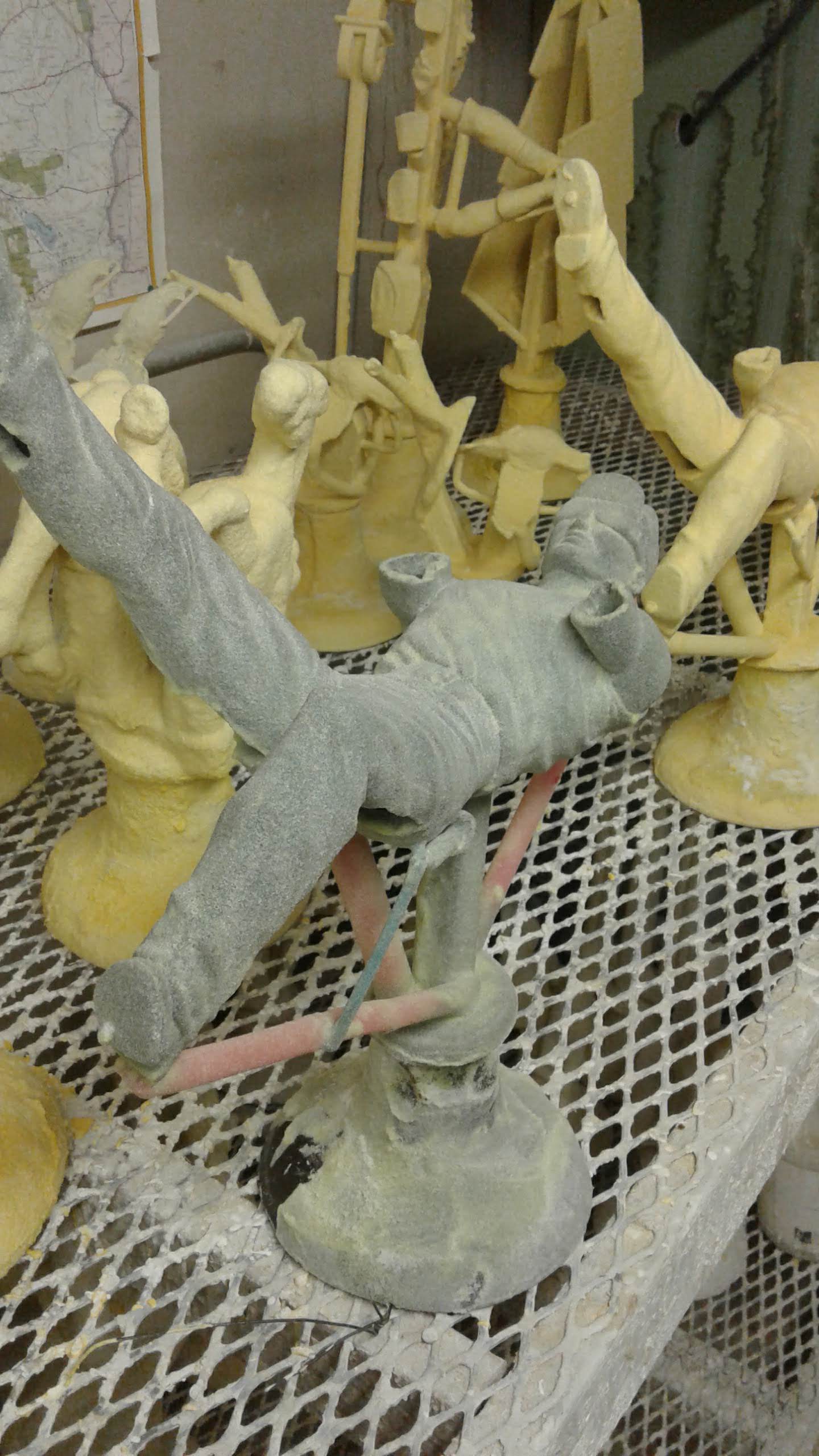
Stage 3: The Lost Wax
Once all the pieces are ready, a “positive” version is created from the rubber by pouring melted wax in a series of layers until the desired thickness is reached. after this layer dries, the rubber mold is removed and a midpoint detailing process takes place. The purpose of this stage is to ensure that all contours and shapes are true to the original clay. The next step consists of beginning the spruing process which is a system of rods applied to the wax pattern. Next, a series of layers of a silica sand and slurry mixture are applied in order to add enough strength for the mold to withstand the temperature from the bronze (these can reach 1800° to 2100° Fahrenheit!).
Stage 4: The Bronze Casting
The bronze casting process is often referred to as “Lost Wax.” This is because during this step the wax inside the mold is melted away. Finally, we get to the pouring of the bronze, a step during which planning and expert knowledge are imperative. This will allow for the optimal flow of bronze in the sculpture thus accurately replicating even the smallest details. Once the bronze has solidified, the outer molds are carefully removed to reveal the sculpture. Lastly, don’t forget that all the separate sections still need to be welded together and sandblasted in order to remove any last materials and residue attached to it. At this stage, the sculpture is ready for the patina to be carefully applied and mounted to the final base.
Stage 5: The Patina Finishing
When the casting is ready for the patina, the casting is then sandblasted so that the surface is clean and even. The casting is then put into a bath of C22 antiquing solution that darkens the metal to a dark grey nearly black color giving the sculpture its base coat of tones for contrast. After rinsing the sculpture with water, a soft industrial scotch-bite pad is used to polish the surface of the sculpture while leaving the recessed areas dark, which creates contrast and helps develop the forms. At times if too much of the dark patina is removed in the polishing, a small brush is used to to paint back in the dark recesses with the original chemical wash. At this point the sculpture has an antique brass look and is left to thoroughly dry. There are lots of different chemicals to get a variety of final color patinas; for copper alloys, such as bronze, exposure to chlorides leads to green, while sulfur compounds tend to brown. In the case of Tim Huhn’s “The Unknown Worker” a deep reach brown with polished brass highlights was desired, so Ferric Nitrate was used to achieve the final patina. In order for the chemical color to bond to the surface of the casting, the sculpture needs to be evenly heated with a blowtorch. While bolted to a metal turntable, the ferric nitrite is put into a large spray gun and is the sprayed onto the casting while rotating it to maintain an even spray. The sculpture is then heated more and the color begins to change. This process is continued until the right color is achieved. It is left to cool down, but while it’s still warm a paste wax is applied to the whole piece using a large soft brush. Once the sculpture is completely cooled down, the last step is to polish the piece using a soft cotton buffer to enhance the luster and sheen in the finished sculpture.
Stage 6: The Finished Bronze
Craftsmanship, integrity and determination are just a few of the core values which Tim Huhn’s “The Unknown Worker” stands for. With such a tenacious and resilient inspiration behind the original oil painting, it became an ideal concept to develop a bronze sculpture. The physical and raw nature of this piece’s composition perfectly lends itself to a tangible and solid sculpture format. This striking piece has introduced a new dynamic element into Tim Huhn’s body of work and elevated the legacy of his work by immortalizing “The Unknown Worker” on bronze.
A special thanks to Genesis Bronze for helping bring Tim Huhn’s vision of “The Unknown Worker” to life in this exceptional sculpture.
Limited Edition of only 75 Hand Cast Bronze Sculptures Mounted on a Black Granite Base
16” Tall by 15” Long by 8” deep
Weighing 32 lbs.
$6,000